激光焊接机焊接缺陷分析?
发布时间:2015-01-20 | 来源:星鸿艺激光焊接运营部 | 分享:
激光焊接机焊接缺陷分析?
一.气孔
(1)气孔的产生粉末冶金材料深熔激光焊接机焊接的最大缺陷是气孔的产生。气孔产生的原因:一方面,由于粉末冶金材料受到烧结和压制条件的限制,不可能达到熔炼材料一样的致密性;另一方面,气孔也是激光焊过程中最常出现的缺陷,由于光致等离子体控制过程中,辅助气体动压力对熔池流动以及小孔内气体的逸出产生影响,它是深熔焊的一个直接结果。气孔不仅影响外观质址,更严重地削弱了焊缝有效承载面积,产生应力集中.从而降低接头强度。常见的气孔形状有线形、圆形、蜂窝形、条虫形等。图5-37和图5-38所示为焊接试件典型的宏观结构,两图中显示了焊接金属中气孔的位置及气孔形成的事实。在图5-37中大多数气孔位于刀头一侧,这表明气孔多来源于刀头。而在图5-38中很多气孔位于焊接金属的根部,这是焊接熔池流动时,浮力与表面张力将金属溶液自中心往外迁移,但重力使流向相反而逆动的缘故。高速激光焊接时,很多气孔封闭在焊接金属中,特别是集中于根部。
在粉末烧结过程中,颗较粘结面的形成通常乳化机乳化泵实验室乳化机乳化机分散机 高剪切乳化机管线式乳化机固液乳化机吸粉乳化机升降乳化机不会导致烧结体的收缩,因而致密化并不标志烧结过程的开始,而只有烧结体的强度增大才是烧结发生的明显标志。随着烧结颈长大,总孔隙体积减小,颗粒较间距离缩短,烧结体的致密化过程才真正开始。因此,粉末的等温烧结过程中,烧结初期顺粒间的原始接触点或面转变成晶体结合,即通过成核、结品长大等原子过程形成烧结颈,在这一阶段中,颗粒内的晶粒不发生变化,颗粒外形也基本未变,整个烧结体不发生收缩,密度增加也极徽
图5-37激光焊接机焊缝的表面 图5-38焊缝的断面
小,但是烧结体的强度和导电性由于颗粒结合面增大而有明显增加;随着烧结时间的延长,原子间颗粒结合面的大量迁移使烧结颈扩大,颗粒间距离缩小,形成连续的孔隙网络;同时,由于晶较长大,晶界越过孔隙移动,而被晶界扫过的地方,孔隙大量消失,烧结体收缩,密度和强度增加是这个阶段的主要特征;烧结后期,闭孔隙球化和缩小。当烧结体密度达到90%以后,多数孔隙被完全分隔,闭孔数且大为增加,孔隙形状趋近球形且不缩小。在这一阶段,整个烧结体仍可缓慢收缩,但主要是靠小孔的消失和孔隙数最的减少来实现的。这一阶段可以延续很长时间,但是仍残留少址的隔离小孔隙不能消除。在烧结过程中,还将出现粉末表面气体或水分的挥发、氧化物的还原和离解、颗拉内应力的消除、金属的回复和再结晶以及聚品长大等。在粉末冶金材料的激光焊过程中,充满金属蒸气和气体的小孔不允许熔池中金属流动造成不规则的小孔形状,在这种不规则的形状快速凝固过程中气孔便产生了。由于焊缝深而窄,冷却速度又快,焊接过程中产生的气体不一定有足够的时间从熔化区中逸出。另外,从熔池中蒸发的金属燕气,或由于熔池不稳定保护气体陷人熔池等也可导致气孔的产生。对于非穿透焊缝,问题比较严重,较易在焊缝的根部出现分散的气孔,这种情况在电子束焊中也常出现,但是由于激光焊的冷却速度快,如果出现气孔,其直径也比传统熔焊由的气孔直径要小。
激光焊接机怎么控制焊接气孔?
由激光焊气孔产品的原理可知,采用合适的刀头配方、烧结工艺及激光焊焊接参数是可以控制气孔的产生的。
1.改善刀头配方。由于刀头是粉末冶金材料,不可避免地存在孔隙,且极易吸附空气中的水分,还有内含的挥发性的填充物,这些都会使其焊接时出现气孔,严重时气孔连成片成为孔洞,从而大大降低焊缝的强度,影响外观质量。在试验中我们发现,加人一定的合金元素能有效地去除气孔,Mn、Si、Ti、Al等与O亲和力强的合金元素在焊接过程中能有效地去除O,减少气孔和孔洞倾向,显著提高焊缝的强度。这一方面是因为这些元素与烧结刀头中的氧元素发生反应,降低了气孔倾向,增加了焊缝有效承载面积;另一方面是因为在焊缝结晶组织中产生了固溶强化、细化晶粒的结果。优化烧结工艺,提高工件的致密性,减少材料内部孔隙,从而减少吸附气体,这也是减少气孔的有效途径。
2.改进刀头烧结工艺。刀头烧结工艺对刀头性能及随后的焊接性能都有很大的影响,致密而力学性能较好的刃头较疏松而力学性能差的刀头在相同的条件下有更好的焊接性。刀头的性能不仅与中间过渡相、骨架有关,还与缺陷有关。在材料一定时,要使刀头性能优良,关键在于设法消除和减少其内部相结构中的孔隙,这可用增大合成压力、选择理想的烧结条件以改善粉末的收编过程、用净化和细化的粉末等方法来达到目的。
随着压力和烧结沮度的提高,粉末体孔隙由大到小,孔隙数且由多到少,孔隙由连通孔隙变化到封闭孔隙,刀头密度增加,粉末颖较间作用面积不断增大,粉末颗粒较之间不断咬合形成很强的粉末颖较间结合力,从而使刀头的硬度、强度增大,具有较好的力学性能。孔隙的缩小、粉末间的相互扩散、相互作用是需要一定时间的。在试验中我们发现,保沮时间太短,刀头很难满足焊接要求.但保温时间太长,生产率低,成本加大。此外,保沮压力也有很重要的影响。在理论上,保温压力越大,刀头的密度越高.但是受石墨模具的限制.过大的压力将使石墨模具的寿命变短甚至扭坏,刀头的密度是不能达到理论值的,刀头内不可避免地存在孔隙。因此,选择合适的压力、烧结温度、保沮时间、粉末混合时间等是保证刀头致密和均匀的重要条件,也是保证有良好焊接性能的前提。
刀头烧结后,必须经过一系列的后续处理,否则也会影响锯片的焊接性能。首先,刀头烧结后必须保证在24h之内焊接,放置时间太长,刀头就容易吸收空气中的水分而受潮,同时也容易氧化变质,激光焊接机焊接时容易出现连续气孔和夹渣现象,从而严重影响焊缝外表美观和焊缝强度;其次,刀头烧结后不可避免地带有飞边,焊接前一定要把飞边清理,否则由于飞边的存在,会使刀头因摆放不好而造成刀头焊偏、焊缝夹渣等现象;最后,烧结后的刀头,其弧度与锯片基体的弧度有一定的差别,同时刀头焊接部位也可能因烧结而产生了一定程度的氧化,所以必须磨削以去除氧化层,同时使焊接部位的弧度与基体一致,以保证激光焊时不会因弧度不一致而造成漏焊或因夹带氧化物而形成夹渣或气孔等。
3.经过近两年的焊接性试验研究,星鸿艺研究中心认为影响焊接性的主要因素是气孔率、热愉人大小和未焊透的情况,焊接性好的合理条件是:热输入应高于0.8kJ/m ,深宽比应大于0.9,焊接金属处的气孔率应小于20%。
激光功率和焊接速度对气孔的影响很大。研究气孔数量和激光功率大小的关系表明,随着激光功率的增加,气孔数增加。据推侧,功率增加使熔化金属被加热到很高温度,产生金属蒸气,使熔池中液体金属变得不稳定产生湍流。通过降低激光功率提高焊接速度可减少金属蒸气的形成,从而抑制气孔的形成。
二.裂纹
裂纹是激光焊接机焊接过程中出现的最严重的缺陷。导致焊接接头开裂的主要因素有两种:冶金因素和力学因素。激光焊的不平衡快速加热与快速冷却的特征,使得整个接头处于复杂的应力状态,构成了接头开裂的力学因素;激光焊又是一系列不平衡工艺过程的综合,在快速冶金凝固过程中,必然会出现成分分布的不均匀及低抗裂性能的淬硬组织等,它们构成了促进裂纹萌生的冶金因素。
三种主要裂纹:结品裂纹、液化裂纹和类再热裂纹,焊缝中心区域是液相结晶最晚的部位,焊缝两侧的柱状晶交汇于此,同时大量低熔点的杂质也堆集于此,形成中心线偏析,从而降低了该处的结合强度,在一定力学条件下,裂纹就产生在这一部位。焊接时,母材熔化后在熔合线处开始结晶凝固成树枝状的一次结晶组织。过渡层一侧的低熔点组分会偏析富集到枝品晶界处,形成液化薄膜。在收缩应力作用下形成裂纹。由于在三品粒交界处,晶粒间相互滑动在三晶点处产生应力集中,裂纹发展到一定程度便会产生楔型开裂。
另外,试验初期用激光束直接对焊胎体材料与钢基。SEM分析发现,焊缝熔合线处存在裂纹,出现裂纹的主要原因是两种材料的性质相差较大,即它们的“冶金相容性差”。另外,母材相差悬殊的线胀系数引起不可消除的应力,熔合线处又存在缺陷,最终导致焊缝熔合线处出现裂纹。这也是在刀头底部待焊处设置过渡层的主要原因。
减少裂纹缺陷的途径有两个方面一是改变焊捧参数,二是根据裂纹的性质合理地改善材料的合金系统,如添加一定的Mn, Mo、w、cr都能有效地防止裂纹,利用变质剂细化焊缝一次结晶组织,对于防止激光焊接机焊缝结晶裂纹也有一定的效果,或者限制有害杂质S, P的含量,Ni含量越高的合金越要注意限制,这是因为Ni与S能形成熔点更低的硫化物及其共晶体的缘故。
推荐阅读/ RECOMMENDED NEWS
- [2019-07-13]手持激光焊机
- [2019-04-26]手持激光焊枪!光纤连续/脉冲手持焊接头
- [2019-04-26]激光焊优势,和相关配置与工艺介绍
- [2019-03-28]铝材激光焊接效果
- [2019-03-09]激光焊接应用前景
- [2019-01-14]激光焊接会越来越普及!
- [2018-12-01]金属工件激光焊接
- [2018-11-15]激光焊接设备多少钱
- [2019-06-29]激光焊接可以用那么保护气,都有什么作用?
- [2019-06-02]农机齿轮采用激光焊接工艺
- [2019-01-24]钣金行业激光焊接解决方案
- [2018-12-03]汽车冷凝器激光焊接解决方案
- [2018-09-01]厨具激光焊接
- [2018-07-07]铜激光焊接
- [2018-06-16]电池盖帽激光焊接
- [2018-06-09]304不锈钢激光焊接
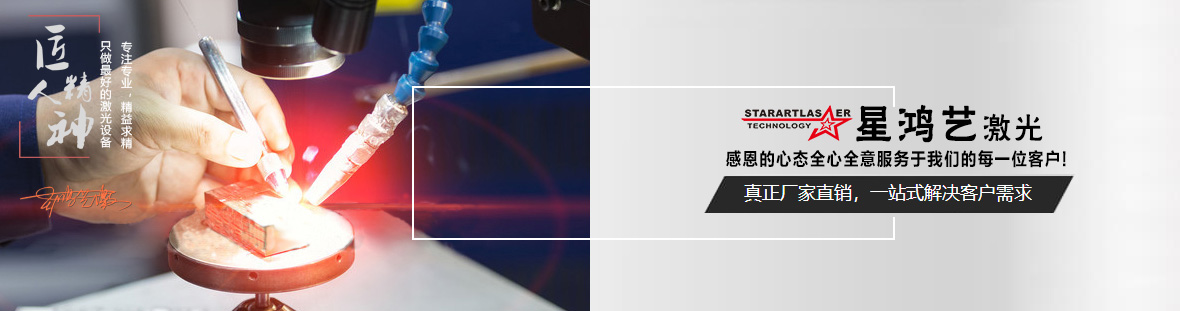
上一页: 最后一页!
下一页: 激光焊接机工艺及参数